Air Blasters & Cannons for General Use

Global Manufacturing's patented Air Blasters, also known as Air Blasters, are blast aerators, which consist of a compressed air reservoir (pressure vessel), with a quick opening valve, that releases the stored air in a sudden, high-energy blast. This blast is directed through a discharge pipe to aerate and dislodge material, and restore flow. In our Direct Blast Air Cannon, the air in the pressure vessel passes directly into the discharge pipe without numerous bends or obstructions in the air path. The unobstructed path is important because the quicker the air discharges, the greater the velocity and force of the blast therefore, the greater the amount of material affected.
When used in combination, multiple Air Cannons will restore flow to hundreds, thousands, or millions of cubic feet of material. Air Cannons are activated manually or by a Programmable Logic Controller (PLC) with graphic Human Machine Interface (HMI) Timer, which controls the firing time interval and sequence of one or more Air Blasters.
Applications:
Air Blasters are an excellent way to solve bulk flow problems for a wide range of material clogs and jams, in hoppers of any size, high temperature applications, and are well suited for large structures of any type. Use Air Blasters when other methods are too expensive, dangerous or destructive, or nothing else works. They are commonly used when it is not practical to apply vibration. For instance, large concrete bunkers and storage piles on the ground are impossible to vibrate, but are common locations of flow problems. They are very effective for cohesive, difficult materials. For instance, wood chips are difficult to dislodge by other means, but respond very well to the quick-release of a powerful blast of air.
Use Air Blasters to periodically aerate material sitting in bins, hoppers, and silos since their blast will lift and separate the material rather than compact it.
Air Cannons Available in Four Designs:
There are four different Air Blaster Designs and up to six model sizes in each group:
- GW - Standard
- GWE - Standard with a built-in patented Quick Exhaust Valve
- G-400 - High Temperature
- Sub-Zero - Tolerates High Temperatures and Sub-Zero Temperatures
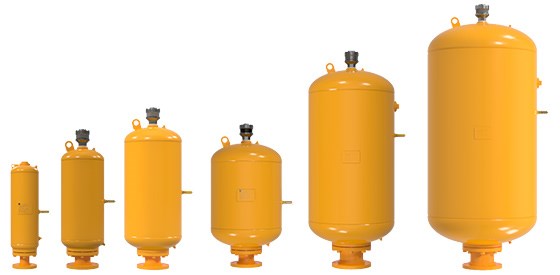
Determining the size and type of the Air Blaster is something Global Manufacturing’s Customer Service can help you do. Please see How to Select and Size an Air Blaster for more information.
The Global Air Cannon Advantage:
Global Manufacturing's patented Air Blasters have been used in the cement, steel, and many other industries for many years. Global Air Blasters have been engineered to improve force output, efficiency, and temperature tolerance. We do not copy others in the industry who have more expensive, heavier, and bulkier external valve-type aerators, but have instead made improvements while minimizing size, weight, maintenance requirements, and manufacturing cost. We believe Global Air Blasters are the best value in the industry today, and we will match their performance and durability against any competitor’s product of any price. Here are the reasons:
- Force Output –
- The force of the air blast is the most important factor in determining the effectiveness of an air cannon. Global Air Blasters produce more force than any other air cannon available today (based on published data). In a direct comparison in our testing facility, under identical conditions, the Global G-400 Air Blasters produced as much as 50% more force than a leading external valve style air cannon. The reason for this is quite simple. Global uses a direct blast design, where the air in the pressure vessel passes directly into the discharge opening with only a single 90º turn. In the external valve designs used today, the air path takes three 90º turns, a total of 270º. This circuitous path slows down the airflow from the pressure vessel significantly, which in turn causes a smaller blast force. This negative effect increases as the volume of air trying to escape increases because flow resistance increases with velocity and a larger volume maintains higher velocity for a longer period. As a result, the larger the pressure vessel used, the more the Global Air Cannons outperform the competition.